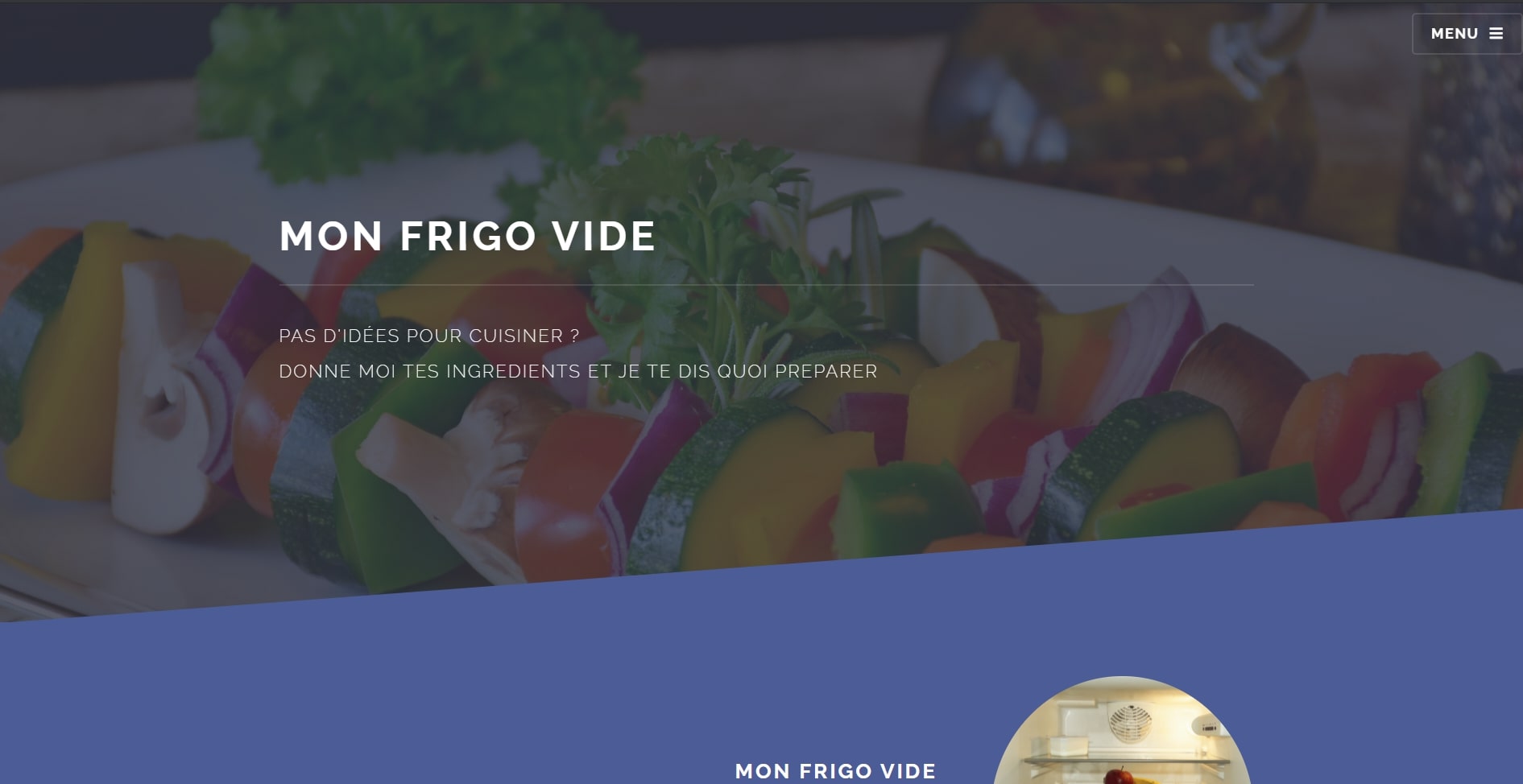
Site de recettes de cuisine
Ou comment les ingénieurs de la marque chinoise ont réussi à rendre un système mécanique plus léger, plus résistant et moins complexe en jonglant avec des schémas et des matériaux. Un tour de force d’ingénierie pour garantir plus de dix ans d’utilisation sans accroc.
Une fois que les premiers écrans souples se sont avérés viables, l’industrie avait encore devant elle un beau casse-tête : comment créer une charnière légère et solide qui transforme le rêve du smartphone pliant en réalité ? Si Samsung a pour l’heure la plus grande expérience dans ce domaine avec ses Galaxy Fold et Flip, qui trustent les premières places des ventes, les marques chinoises ont récemment accéléré dans le domaine. Avec comme principal protagoniste Honor et son Magic Vs, le premier modèle que la marque a décidé de commercialiser en France et qui représente sa seconde génération de terminaux pliants.
Lire aussi : Un bijou mécanique : on a essayé le Magic Vs, le smartphone pliant de Honor (novembre 2022)
Entre son premier modèle (Magic V) et ce Magic Vs, une toute petite année d’écart. Avec les traditionnels changements de composants comme le processeur, ou encore les évolutions d’écran. Mais la plus importante avancée technique qu’apporte ce Magic Vs est la partie mécanique de l’appareil, à savoir la charnière. Après que l’industrie a passé des années à simplifier les smartphones pour retirer toutes les parties mobiles, analogiques et mécaniques des smartphones traditionnels– désignés dans l’industrie sous le nom de candy bar – voilà que les terminaux pliants réintroduisent de l’encombrement et une potentielle fragilité. Comment se développe une telle mécanique ? Quels sont les enjeux et axes d’améliorations d’années en années ? Nous avons pu parler à deux ingénieurs haut placés d’Honor pour parler des défis déjà relevés… et un peu du futur.
Bin « Samuel » Deng (en photo ci-dessus) et Yongtao Yang ne sont pas des perdreaux de l’année. Respectivement président du département R&D -passé par Samsung et Huawei- et directeur de la division produit de Honor, les deux hommes nous ont accordé un entretien exclusif pour parler de la pièce d’orfèvrerie que représente cette charnière. Et ils posent directement la problématique principale qui les anime : « Comment rendre les smartphones pliants plus fins, plus légers et plus solides ? ». Une très bonne question dont la réponse ne se trouve pas uniquement dans leur labo : « Ce genre de développement implique de parler avec beaucoup de partenaires. Et beaucoup de ressources en interne », racontent les deux hommes.
Si vous avez la chance de tenir un Magic Vs, regardez le mécanisme de près et appréciez le fait qu’il a fallu une vraie petite armée pour la développer. « La charnière du Magic V représente environ 120 personnes travaillant à plein temps pendant une année entière et pas moins de 57 brevets », explique Bin Deng d’un air assuré.
La prouesse intergénérationnelle chez Honor tient en deux chiffres : la charnière est passée de 92 à 4 composants ! Une réduction de complexité extrêmement difficile à réaliser. Tant du point de vue des matériaux, de la conception mécanique que de l’assemblage ou de la vérification. « Les deux premiers défis sont le choix des bons matériaux et de la bonne structure mécanique », expliquent les deux hommes. « Dans un premier temps, nous avons déjà limité le nombre de composants en acier, que nous avons accompagnés de pièces en polymère très léger et résistant ». Ici, Honor a d’ailleurs fait un choix clair : il a limité la charnière aux seules positions ouverte ou fermée.
Lire aussi : Pour son futur smartphone pliant, Microsoft prend la bonne décision (janvier 2023)
« En réduisant l’épaisseur d’un millimètre, le défi pour nous était aussi de faire mieux en matière de durabilité. Il fallait trouver des matériaux qui soient plus légers, mais aussi plus résistants que ceux de la génération précédente ». Un travail de titan qui leur a permis de passer de 200.000 cycles d’ouverture garantis à 400.000. « En réalité, nous estimons que la charnière peut aller jusqu’au demi-million de cycles d’ouverture/fermeture. Mais nous préférons prendre une marge de sécurité. Car 400.000 cycles, c’est déjà plus d’une centaine de cycles par jour pendant dix ans ! », ajoutent les deux hommes.
Qui ajoutent rapidement que « ce travail s’est effectué avec tous nos partenaires et fournisseurs ». Pourtant, un travail fondamental est le fruit de l’unique travail du géant chinois de l’électronique : le montage et la qualification.
Parfois, les prouesses sont là où on les attend le moins. En scrutant les nombreux détails de la charnière nue que les ingénieurs nous ont laissé manipuler, nous avons demandé ce qui la rendait unique, puisque l’entreprise travaille avec des partenaires qui ne sont peut-être pas tous exclusifs. Et les ingénieurs de répondre tout de go « l’assemblage et la vérification. Nous avons réussi à mettre au point en interne une méthode d’assemblage des pièces en une seule opération au lieu de plusieurs, ce qui est un grand bond en avant. De plus, nous avons conçu et fabriqué nos propres machines pour la vérification et la qualification de la pièce », se félicitent-ils.
Ce dernier procédé est clé dans la confiance que l’entreprise va pouvoir mettre dans sa pièce. C’est grâce à cela que le nombre de cycles a été garanti. Car oui, interrogé par nos soins sur la nature des 400.000 cycles – ont-ils été extrapolés ou mesurés – la réponse tombe immédiatement, sans le moindre doute : « Il s’agit bien d’une mesure », assurent-ils.
Quant à la méthode d’assemblage de la charnière, il ne faut pas être grand clerc pour comprendre le bénéfice que cela représente pour l’entreprise qui dispose de ses propres usines de fabrication de terminaux : cela réduit le temps nécessaire pour monter un téléphone. Ce qui a un impact immédiat sur le prix final actuel… et futur.
Honor construit des smartphones pour les vendre. Et ce fort investissement dans la conception de terminaux pliants et dans la simplification de leur assemblage montre que l’entreprise croit dans le format. « Les smartphones pliants sont les nouveaux terminaux haut de gamme. Et s’ils ne devraient pas remplacer les smartphones normaux, ils sont un segment important du futur », assurent les deux hommes.
Un des leviers pour le développement du genre, est « de rendre les appareils moins chers ». Pour réussir leur pari, les ingénieurs pensent qu’il faut aller encore plus loin. Sans nous donner les détails exacts de la troisième génération de charnière qui devrait arriver d’ici un peu moins d’un an, ils nous ont dressé leurs ambitions. « Nous voulons développer des terminaux pliants qui soient aussi fins et aussi légers que les smartphones normaux ». Une gageure qui implique de nombreux défis… et de reprendre le travail presque à zéro. « La réduction de l’épaisseur et du poids va nous obliger à concevoir un nouveau design, à trouver de nouveaux matériaux et concevoir de nouveaux procédés de fabrication », lâche M. Deng.
La recherche des bons matériaux est clé. « Il faut faire très attention aux forces de friction qui finissent pas user les plastiques et polymères plus vite que le métal », nous assure-t-on. Mais le métal reste lourd. Enfin pas tous les métaux : interrogés à propos de l’usage du titane, les deux ingénieurs valident « travailler dessus. Parmi les candidats possibles, le titane est effectivement une piste que nous explorons. Ainsi que les matériaux à mémoire de forme ». Une exploration qui ne se borne pas à une simple charnière. « Nous regardons aussi les multiples charnières, mais pour cela, nous devons nous interroger sur les usages. C’est-à-dire non seulement sur la partie matérielle, mais aussi sur la solution complète, avec le logiciel ».
Lire aussi : Les smartphones pliants sont-ils condamnés à rester des produits de niche ? (octobre 2022)
Avec le prototype de PC à écran déroulant présenté au MWC de Barcelone, nous avons donc demandé si Honor travaillait à d’autres appareils que des smartphones avec des charnières. « La technologie des charnières peut être bien sûr être adaptée à d’autres tailles et nous sommes persuadés que ces mécanismes vont continuer de se diffuser. Si nous explorons plusieurs scénarios comme des mécaniques à plusieurs charnières, nous n’avons pour l’heure aucun plan de développement de PC ou de tablette. Les smartphones, c’est suffisant pour le moment ! ».
Aucun commentaire n'a été posté pour l'instant.